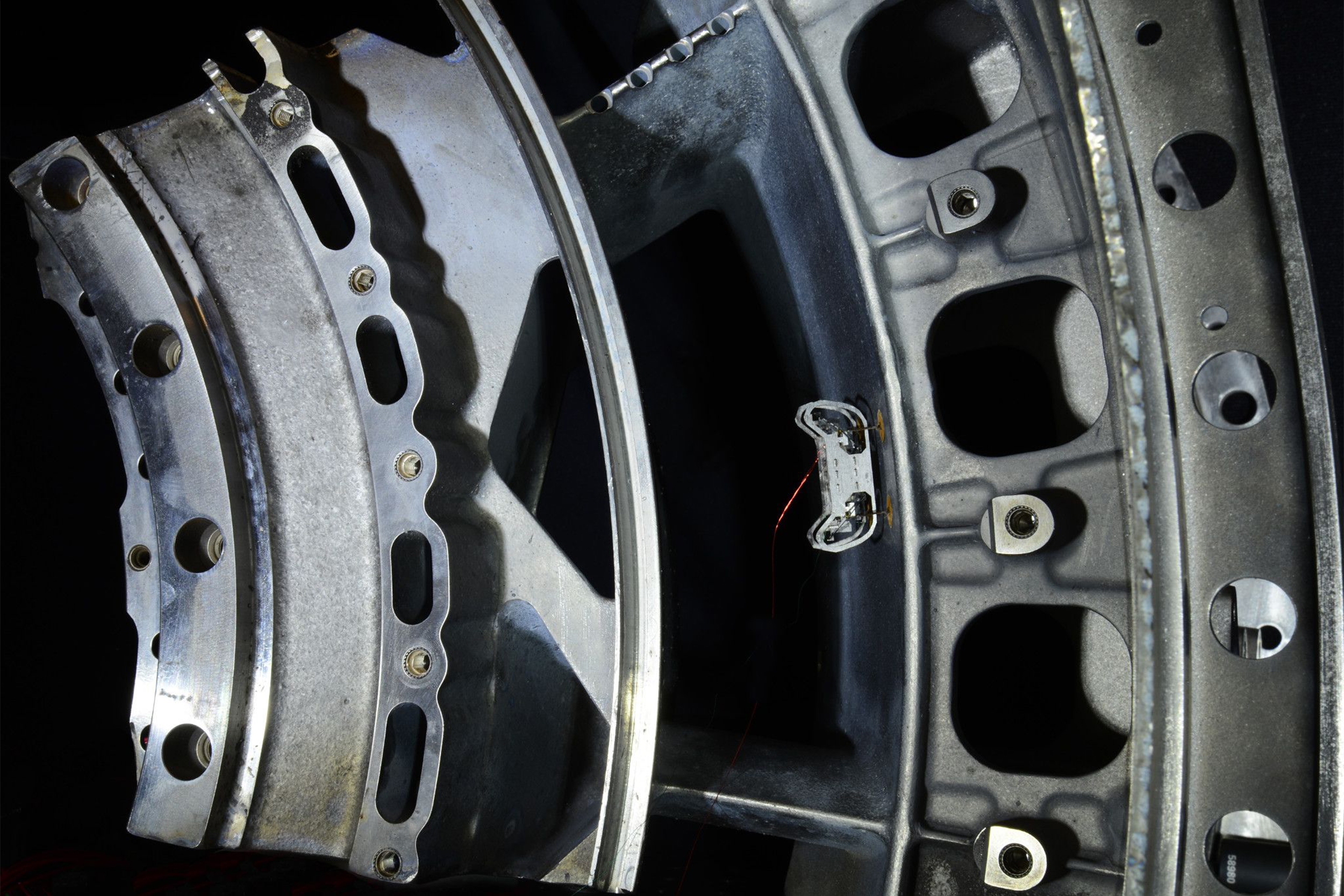
HAMR-E uses electroadhesive pads on its feet and a special gait pattern to climb vertical, inverted, and curved surfaces, like the inside of this jet engine.
Credit: Wyss Institute at Harvard University
Robots with sticky feet can go where humans can’t
Army of micro-robots could inspect complex machines without dismantling them
Jet engines can have up to 25,000 individual parts, making regular maintenance a tedious task that can take over a month per engine. Many components are located deep inside the engine and cannot be inspected without taking the machine apart, adding time and costs to maintenance. This problem is not confined to jet engines, either; many complicated, expensive machines like construction equipment, generators, and scientific instruments require large investments of time and money to inspect and maintain.
To make this upkeep easier, faster, and cheaper, researchers at Harvard University’s Wyss Institute for Biologically Inspired Engineering and John A. Paulson School of Engineering and Applied Sciences (SEAS) have created a micro-robot whose electroadhesive foot pads, origami ankle joints, and specially engineered walking gait allow it to climb on vertical and upside-down conductive surfaces, such as the inside walls of a commercial jet engine. The work is reported in Science Robotics.
“Now that these robots can explore in three dimensions instead of just moving back and forth on a flat surface, there’s a whole new world that they can move around in and engage with,” said first author Sébastien de Rivaz, a former research fellow at the Wyss Institute and SEAS who now works at Apple. “They could one day enable noninvasive inspection of hard-to-reach areas of large machines, saving companies time and money and making those machines safer.”
The new robot, called HAMR-E (Harvard Ambulatory Micro-Robot with Electroadhesion), was developed in response to a challenge issued to the Harvard Microrobotics Lab by Rolls-Royce, which asked if it would be possible to design and build an army of micro-robots capable of climbing inside parts of its jet engines that are inaccessible to human workers. Existing climbing robots can tackle vertical surfaces, but experience problems when trying to climb upside-down, as they require a large amount of adhesive force to prevent them from falling.
The team based HAMR-E on one of its existing micro-robots, HAMR, whose four legs enable it to walk on flat surfaces and swim through water. While the basic design of HAMR-E is similar to HAMR, the scientists had to solve a series of challenges to get HAMR-E to successfully stick to and traverse the vertical, inverted, and curved surfaces that it would encounter in a jet engine.
First, they needed to create adhesive foot pads that would keep the robot attached to the surface even when upside-down, but release to allow the robot to “walk” by lifting and placing its feet. The pads consist of a polyimide-insulated copper electrode, which enables the generation of electrostatic forces between the pads and the underlying conductive surface. The foot pads can be released and re-engaged easily by switching on and off the electric field, which operates at a voltage similar to that required to move the robot’s legs, thus requiring very little additional power. The electroadhesive foot pads can generate shear forces of 5.56 grams and normal forces of 6.20 grams — more than enough to keep the 1.48-gram robot from sliding down or falling off its climbing surface. In addition to providing high adhesive forces, the pads were designed to flex, thus allowing the robot to climb on curved or uneven surfaces.
The scientists also created new ankle joints for HAMR-E that can rotate in three dimensions to compensate for rotations of its legs as it walks, allowing it to maintain its orientation on its climbing surface. The joints were made of layered fiberglass and polyimide and folded into an origami-like structure that lets all the legs rotate freely, and passively align with the terrain as HAMR-E climbs.
Finally, the researchers created a special walking pattern for HAMR-E, as it must have three foot pads touching a vertical or inverted surface at all times to keep it from falling or sliding off. As one foot releases from the surface, swings forward, and reattaches, the remaining feet stay attached to the surface. At the same time, a small amount of torque is applied by the foot diagonally across from the lifted foot to keep the robot from moving away from the climbing surface during the leg-swinging phase. This process is repeated for the three other legs to create a full walking cycle, and is synchronized with the pattern of electric-field switching on each foot.
When HAMR-E was tested on vertical and inverted surfaces, it was able to take more than 100 steps in a row without detaching. It walked on inverted surfaces at speeds comparable to other small climbing robots and slightly slower than other climbing robots on vertical surfaces, but was significantly faster than other robots on horizontal surfaces, making it a good candidate for exploring environments that have a variety of surfaces in different arrangements in space. It is also able to perform 180-degree turns on horizontal surfaces.
HAMR-E also successfully maneuvered around a curved, inverted section of a jet engine while staying attached, and its passive ankle joints and adhesive foot pads were able to accommodate the rough and uneven features of the engine surface simply by increasing the electroadhesion voltage.
The team is continuing to refine HAMR-E, and plans to incorporate sensors into its legs that can detect and compensate for detached foot pads, which will help prevent it from falling off vertical or inverted surfaces. HAMR-E’s payload capacity is also greater than its own weight, creating the possibility of carrying a power supply and other electronics and sensors to inspect various environments. The team is also exploring options for using HAMR-E on nonconductive surfaces.
“This iteration of HAMR-E is the first and most convincing step toward showing that this approach to a centimeter-scale climbing robot is possible, and that such robots could in the future be used to explore any sort of infrastructure, including buildings, pipes, engines, generators, and more,” said corresponding author Robert Wood, a founding core faculty member of the Wyss Institute and the Charles River Professor of Engineering and Applied Sciences at SEAS.
“While academic scientists are very good at coming up with fundamental questions to explore in the lab, sometimes collaborations with industrial scientists who understand real-world problems are required to develop innovative technologies that can be translated into useful products. We are excited to help catalyze these collaborations here at the Wyss Institute, and to see the breakthrough advances that emerge,” said Wyss Founding Director Donald Ingber, the Judah Folkman Professor of Vascular Biology at Harvard Medical School and the Vascular Biology Program at Boston Children’s Hospital, and professor of bioengineering at SEAS.
This study was co-authored by Benjamin Goldberg, Neel Doshi, Kaushik Jayaram, and Jack Zhou from the Wyss Institute and SEAS.
Support for this research was contributed by the Wyss Institute for Biologically Inspired Engineering at Harvard University, Rolls-Royce, and the U.S. Army Research Office.