Onward and upward, robots
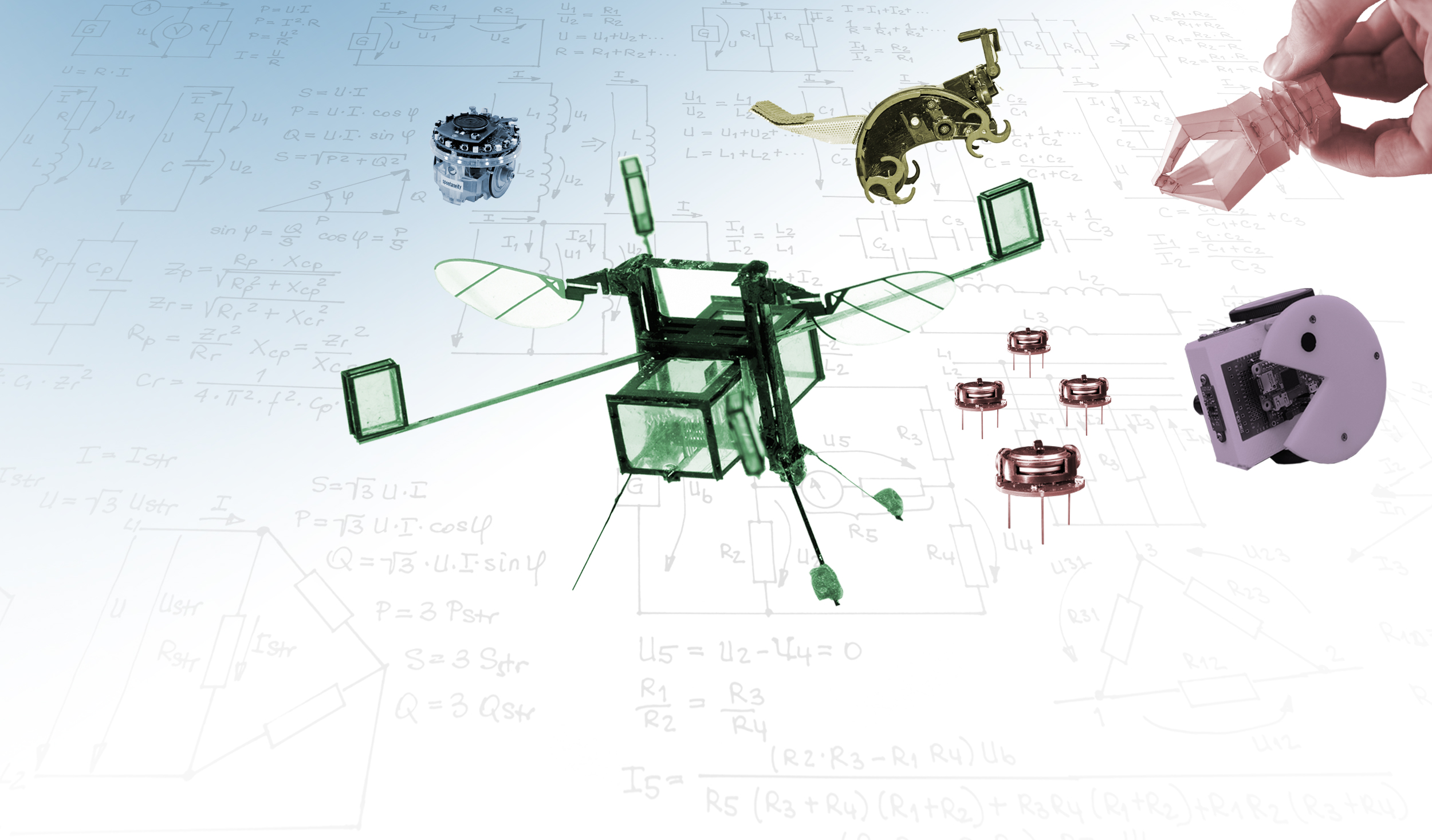
Harvard scientists help drive new age of machines, aiming for transformative impact in medicine, on Main Street, and beyond
EDGE OF DISCOVERY
First in a series of articles on cutting-edge research at Harvard.
On a visit to one Harvard robotics lab, the sewing machines stand out, while the head of another explains how and why lab members are studying termites in Namibia.
Welcome to the new age of machines, in which scientists with seemingly disparate talents are using cutting-edge materials, cheap sensors, 3-D printing, and powerful computers to accelerate advances in robotics.
Prior innovations transformed the factory and warehouse, but those robots work best in controlled environments, usually out of public view. For researchers at Harvard and elsewhere, one new target is Main Street. “We were promised these things by sci-fi for 50 years,” said Robert Wood, Charles River Professor of Engineering and Applied Sciences. “So where are the robots?”
The next generation will venture widely into the real world, trekking through forests and fields, driving around town, and covering chores. Major retailers such as Amazon are frank about their desire to deliver packages with drones, automakers want your car to steer itself, and for those who can’t find the time to vacuum the living room rug, there’s a robot for that.
But tomorrow’s machines won’t just drop you off, deliver your packages, and clean your house. They will also search for disaster victims and help farm food, experts say. They’ll fight wars, brace limbs, and heal hearts.
“Certainly, the technology is now there, and there’ve been some developments over the last decade that allow us to build robots good enough to deal with the real world,” said Robert Howe, the Abbott and James Lawrence Professor of Engineering.
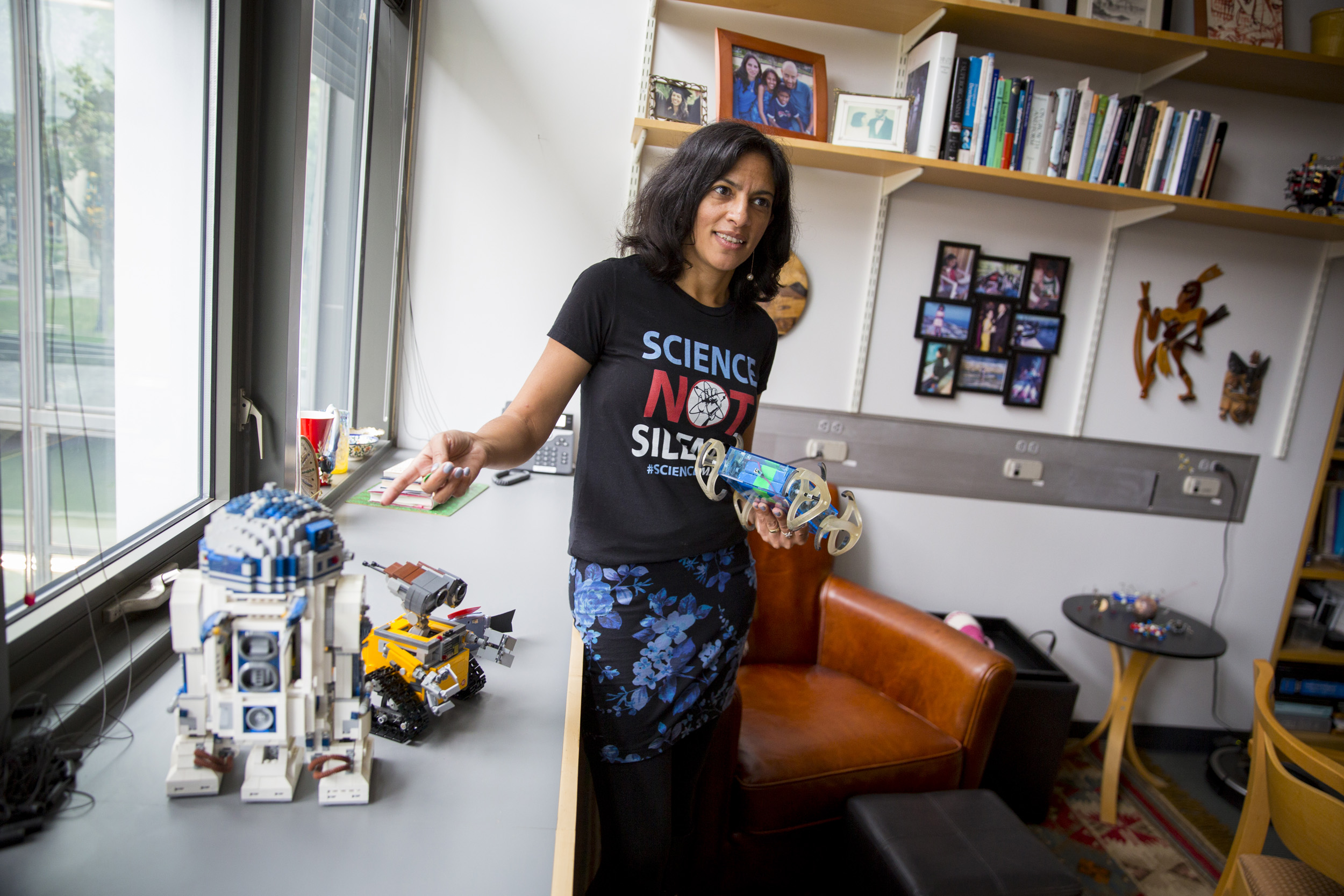
Rose Lincoln/Harvard Staff Photographer
“We build the kinds of robots that people haven’t imagined yet. Little bees that fly, thousands of robots you buy, robots that build by climbing over things, robots that you wear.”
– Radhika Nagpal, pictured above
Thousands of Kilobots from Radhika Nagpal’s lab work together to complete tasks.
Video by SEAS
Momentum builders
Harvard’s recent efforts in robotics have enlivened a historically quiet scene. George Whitesides, the Woodford L. and Ann A. Flowers University Professor, noted that his own soft-robot breakthroughs have as much to do with Harvard’s strength in soft-matter physics and with colleagues’ microfluidics work as with robotics.
Some of the earliest work on soft robots was done by Japanese researchers in the 1990s. More recently, innovations by Whitesides, Wood, and colleagues like Conor Walsh have advanced the field, paving the way for machines whose design and characteristics, rather than hard gears and levers, regulate movement.
“We replace controls by the properties of materials,” Whitesides said, holding up a starfish-shaped rubber gripper that clenches when air is pumped into its arms. “These things tend to curl from the tip — that’s a controllable thing. It would be essentially impossible to replicate without all kinds of things in hard robots.”
The work has led to robots that can function despite being run over by a car, that creep and crawl instead of rolling or marching. It has led to research on new manufacturing techniques, such as 3-D printing advances in the lab of Jennifer Lewis, Hansjörg Wyss Professor of Biologically Inspired Engineering. It has also led to a collaboration with National Geographic on underwater graspers capable of collecting samples of delicate coral, and to the development of a company, Soft Robotics, to commercialize flexible grippers that can handle an array of products — on a farm, in a warehouse, or on an assembly line.
Researchers from the Robert Wood lab tested this untethered robot in snow, submerged it in water, walked it through flames, and even ran it over with a car. After each experiment, it emerged unscathed.
Director and editor: Ned Brown/Harvard file video
“The transition to market has been an interesting one,” said Whitesides. “What’s turned out to be the initial application is for things I didn’t know existed as problems. … It made it from the lab to commercial [applications] faster than anything I’ve ever been involved in.”
Companies like Soft Robotics provide a relatively straightforward measure of robotics progress at Harvard, according to Sam Liss, executive director of strategic partnerships for Harvard’s Office of Technology Development.
“The level of startup formation is remarkable,” he said. “Within just the last few years, we’ve seen the launch of Soft Robotics, RightHand Robotics, and Root Robotics, with more to follow. This is a sea change at Harvard. It speaks to not only the significance of the research, but also to our faculty’s focus on translating this research into products that will have impact.”
Growth in robotics at Harvard has been driven by the Paulson School of Engineering and Applied Sciences, and the Wyss Institute for Biologically Inspired Engineering. Researchers say deeper investment in robot-building tools and facilities has made an enormous difference to faculty, students, and fellows.
“Especially for the things I do, it’s really important to have those tools accessible for students and postdocs,” Wood said. “SEAS and the Wyss Institute have done a very good job of investing in some of those areas. We don’t really lack anything in that regard.”
Team efforts
Harvard has a small core of less than a dozen robotics specialists who collaborate regularly and rely heavily on one another’s expertise. The focus is on land, sea, and air machines that can work closely with humans, often in medical settings, and which think and behave in ways that reflect the innovative drive of their developers.
“We build the kinds of robots that people haven’t imagined yet,” said Radhika Nagpal, the Fred Kavli Professor of Computer Science. “Little bees that fly, thousands of robots you buy, robots that build by climbing over things, robots that you wear. Our strength in some ways is the wild and crazy robots. Robots that are more like animals than they are wheeled cars.”
One example is the RoboBee. Developed by Wood and controlled by Nagpal’s software, the insect-sized flying robot has wide potential as a surveying tool, with the ability to collect images and data from natural disasters, crop-disease outbreaks, even war zones. Small enough that mechanical levers, gears, and other off-the-shelf components were impractical, the machine demanded advances in areas beyond robotic design.
“With RoboBees, no component was off the shelf,” said Wood. “We had to invent everything from the ground up: new manufacturing methods, new actuation, sensing, computing architecture, new energy storage — then [with] Radhika, new algorithms to control behavior. A lot of the platforms we work on don’t exist and we have to develop them from scratch. We really like those, not just because of the cool factor but because of the tech fallout along the way.”
Sensors and actuators light enough to fly on a robotic insect, for example, might be useful in biomedical devices in which size is crucial, like those used in minimally invasive procedures, said Wood.
“We’re taking all these technologies developed from RoboBees, blending them with soft robotics to make new tools for endoscopy and come up with techniques for procedures that are otherwise quite hard to do,” he said.
A central attraction of medical robotics is the chance to make a positive impact in people’s lives, said Walsh, the John J. Loeb Associate Professor of Engineering and Applied Sciences, whose lab-sewn soft-robotic exosuit may one day help stroke patients walk with greater ease. With Harvard Medical School and its 16 affiliated hospitals and research institutions nearby, robotics faculty are well-positioned to determine patient needs that robots might fill, and to collaborate with physicians on setting solutions in motion.
For example, in work backed by the National Institutes of Health, Howe and Pierre Dupont, chief of pediatric cardiac-bioengineering at Harvard-affiliated Boston Children’s Hospital, have collaborated for years on robotic technology for beating-heart surgery. They are currently working on complementary approaches for controlling how robotic catheters compensate for the motion of a beating heart. Success would allow patients to skip open-heart surgery in favor of a minimally invasive procedure.
“It would be so much better for the patient — less trauma, less risk,” said Dupont. “We’re trying to develop technology clinicians haven’t dreamed of yet.”
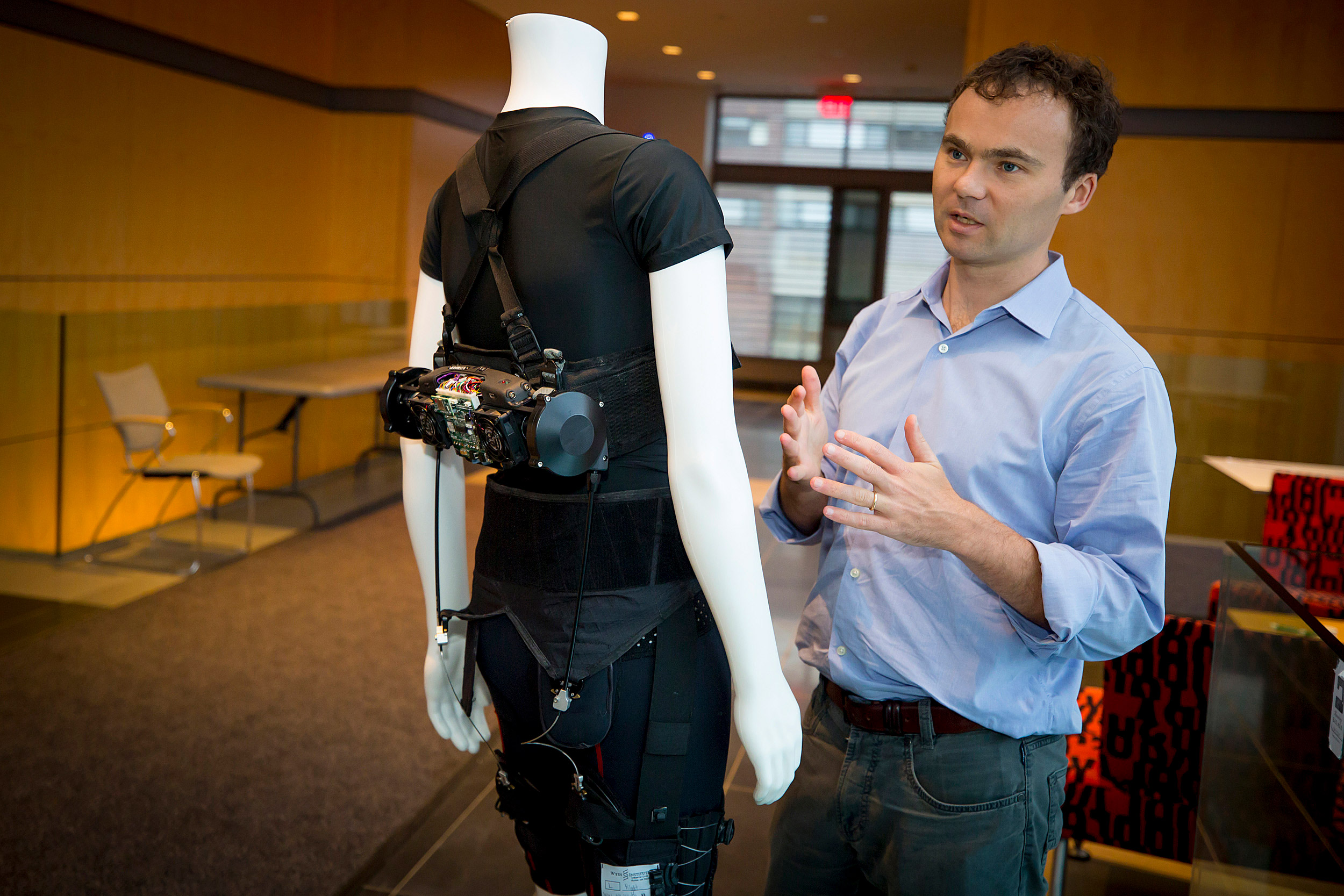
Photos by Rose Lincoln/Harvard Staff Photographer
“I see opportunities for types of things we’re doing to actually make a difference in people’s lives.”
Conor Walsh, above
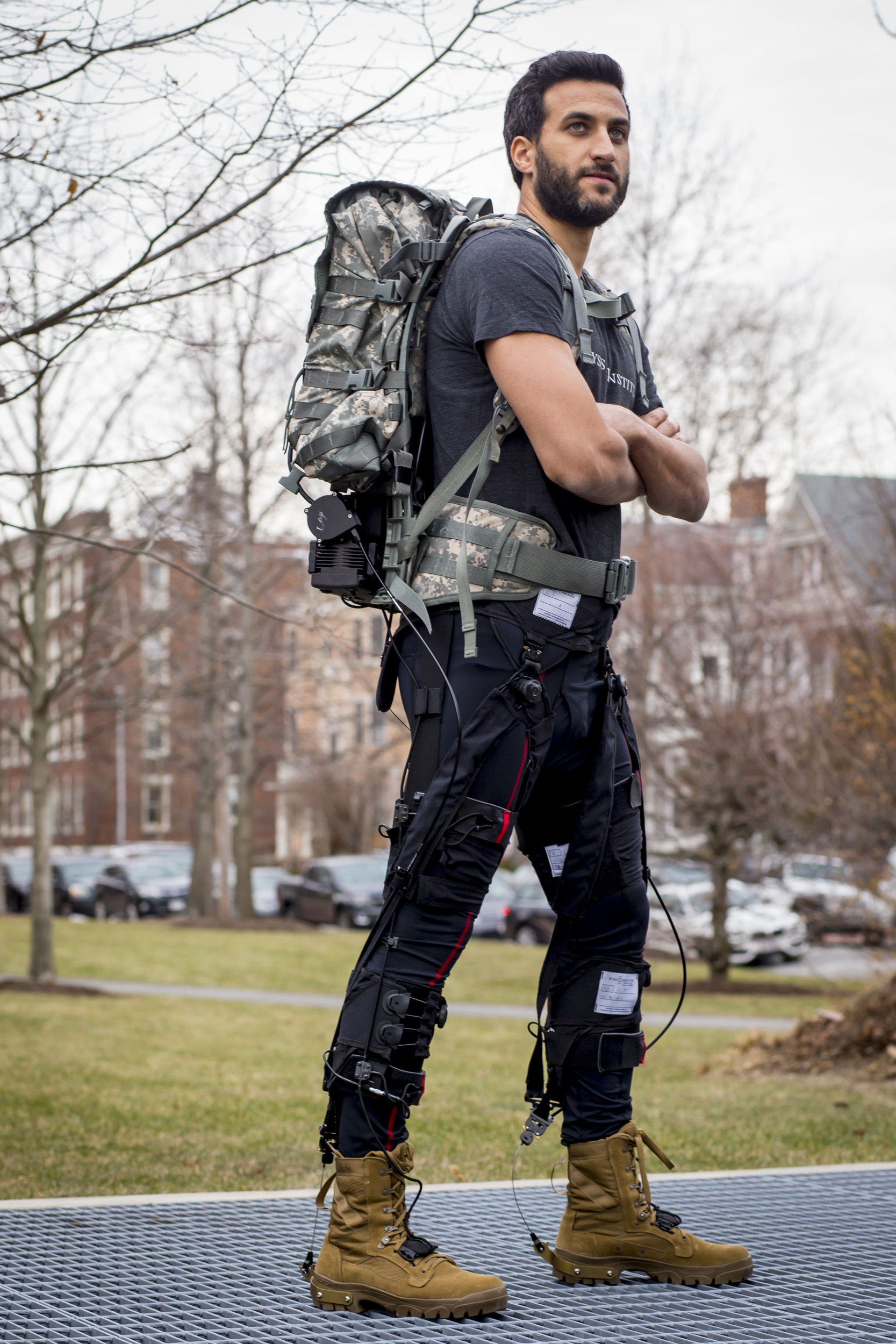
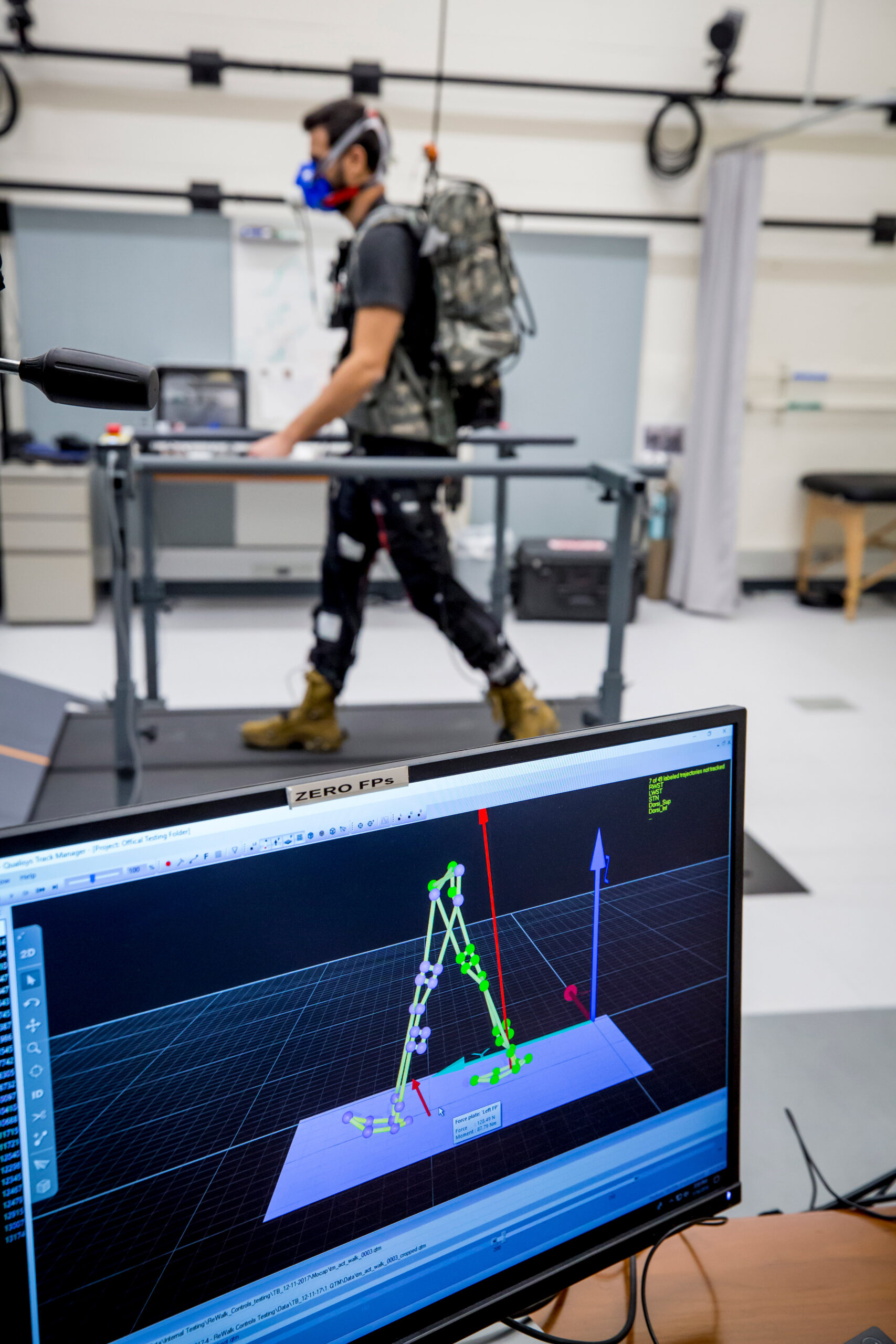
Nikos Karavas, controls engineer, tests a fabric robotic exosuit in Conor Walsh’s lab.
Meanwhile, Walsh’s exosuit technology has been licensed to ReWalk Robotics, whose plan to put a product in clinical trials this year is a first step in a strategy to bring the machine from concept to market in less than five years.
“I see opportunities for types of things we’re doing to actually make a difference in people’s lives,” Walsh said.
The medical applications of Walsh’s work — which includes devices to counter heart failure, improve arm function for patients with spinal-cord injury, and boost post-stroke mobility — owe to early and ongoing support from the Defense Advanced Research Projects Agency (DARPA), whose focus is on an exosuit that might ease the burden of 100-pound troop packs.
Soft exosuits combine properties of functional apparel with precise placement of cables and motors to strategically assist movement.
“The concept of going with a soft system is you can make the system very lightweight, very nonrestrictive, that has a minimal impact on the biomechanics of a person while they walk and is able to deliver a boost in addition to what the wearer’s muscles are normally doing,” Walsh said. “The question then is … can we have a positive effect on a person’s mobility?”
So far, in tests on treadmills and on miles-long military hikes, that effect has been measured at 15 percent. In addition, Walsh’s team has demonstrated in experiments with stroke patients that the exosuit can help users clear the ground and push off at the ankle, reducing functional asymmetry between limbs and increasing walking efficiency. Key challenges going forward will include minimizing weight while maximizing assistance and syncing the suit with natural movements.
“Is this in synergy with this person?” Walsh said. “Because if you get the timing wrong, our studies have shown you don’t get anywhere near the benefit you can get, but if you get it just right you can really make a big difference to a person.”
Cassie robot, Scott Kuindersma lab.
Director and editor: Ned Brown; cinematographer: Kai-Jae Wang/Harvard Staff
Behavior issues
As important as how a machine moves is how it thinks, a reality that Harvard researchers themselves are thinking hard about. Scott Kuindersma, an assistant professor of engineering and computer science and director of the Harvard Agile Robotics Lab, has his sights set on ramping up control systems so that robots reach their full potential.
“In my opinion, physically capable robots are already here,” said Kuindersma. “But those robots struggle to perform at their dynamic limit and lack robustness in realistic environments. That’s primarily a computational problem.”
A recent arrival at Kuindersma’s lab is Cassie, a two-legged walking robot that looks something like an ostrich. Designed by Agility Robotics, Cassie is an example of advanced hardware that Kuindersma thinks can perform better.
“[Cassie] is using a controller the company has developed,” Kuindersma said. “We will promptly delete this. Our goal is to develop algorithms that push locomotion performance beyond state-of-the-art, using this as an experimental platform. A major milestone for us would be to demonstrate high-speed locomotion outdoors, using visual sensor feedback at high rates to plan dynamic walking.
“Think about a mountain goat,” he said. “They can scurry up a cliff face, making fast decisions on where to place their feet on very geometrically complex terrain. We’re interested in creating algorithms that can achieve that kind of performance with robots.”
While Kuindersma is exploring how to better control complex individual actions, Nagpal is investigating the opposite approach: how to drive complex behavior in groups of simple individuals.
“My lab has always had this theme of complexity through simplicity,” Nagpal said. “No matter what kind of agent — ant, human being, or robot — there’s always a limit to what an individual can do. We transcend that by having groups. … Animals that have evolved to work in groups really take advantage of these things.”
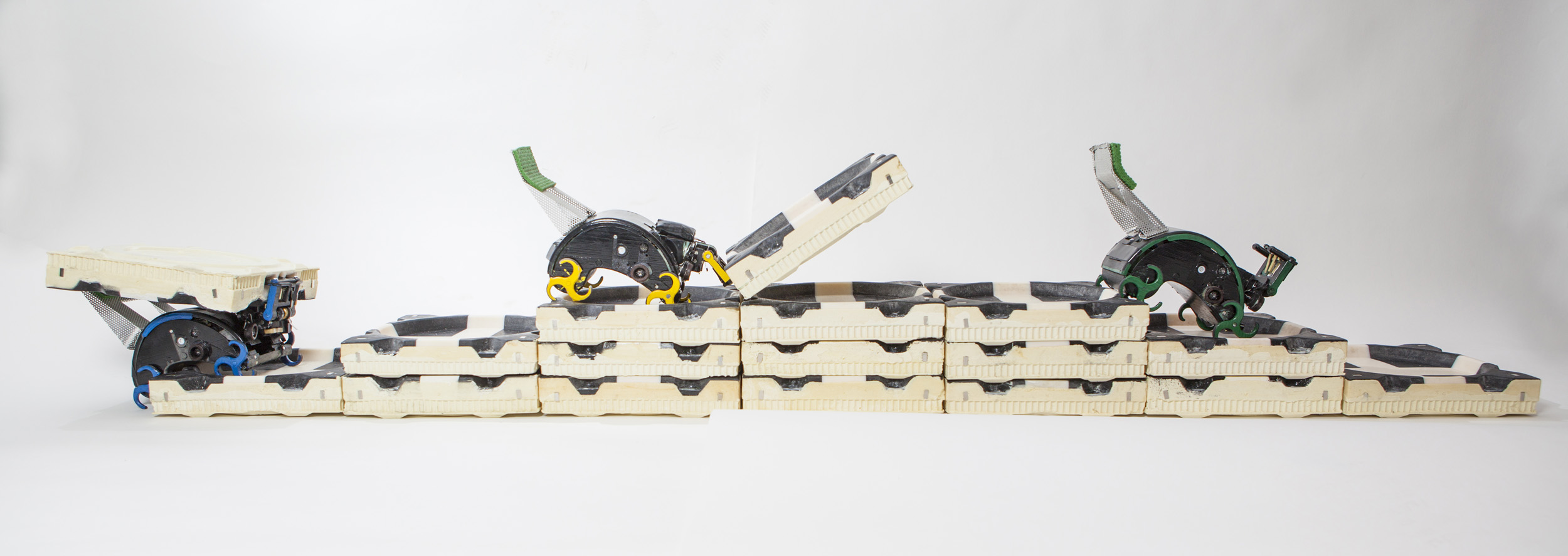
Inspired by the way termites in Namibia cooperate socially to build mounds, the Termes robots can build towers, castles, and pyramids out of foam bricks. In the future, researchers say, they could lay sandbags in advance of a flood or even perform simple construction tasks on Mars.
Photos by Eliza Grinnell
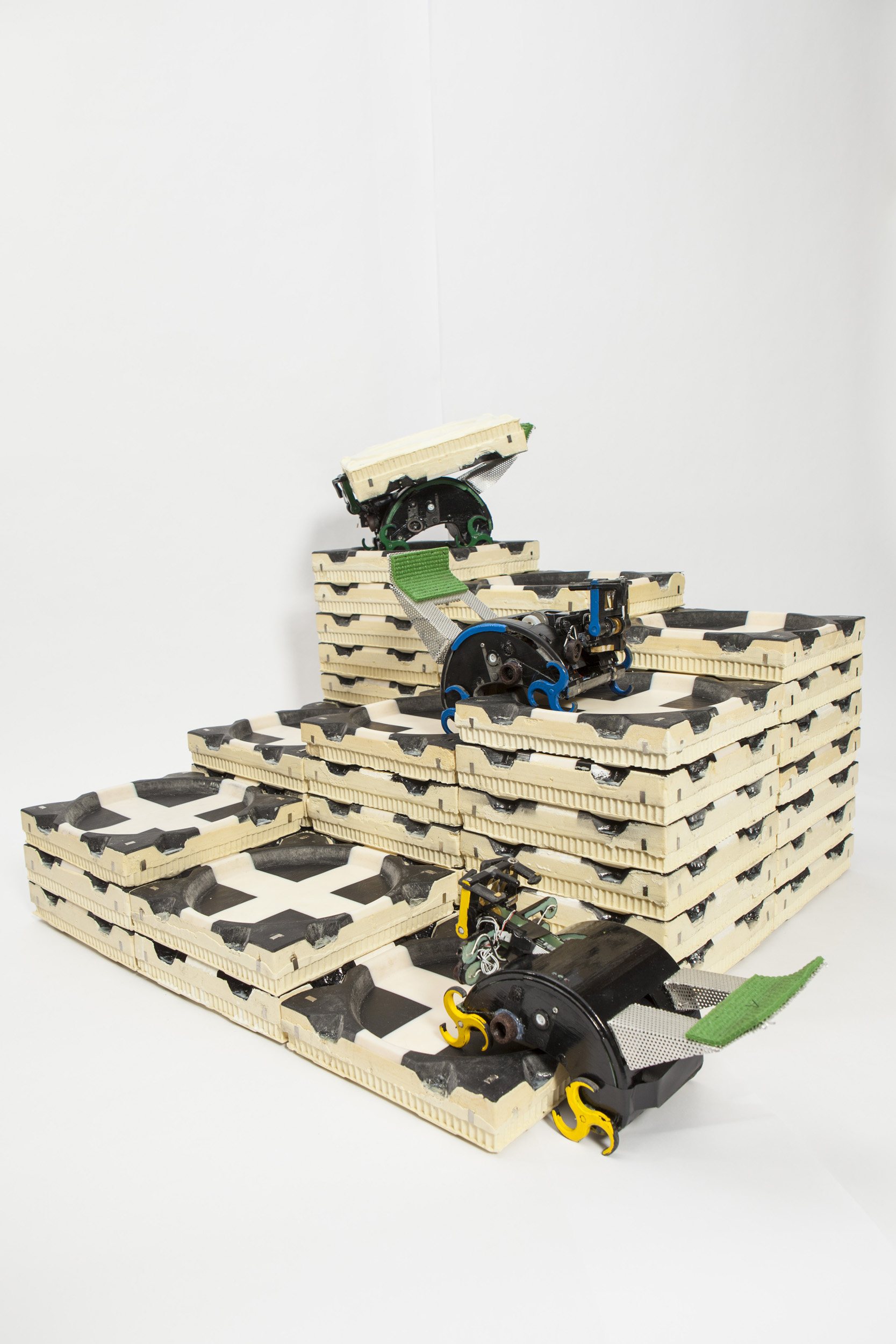
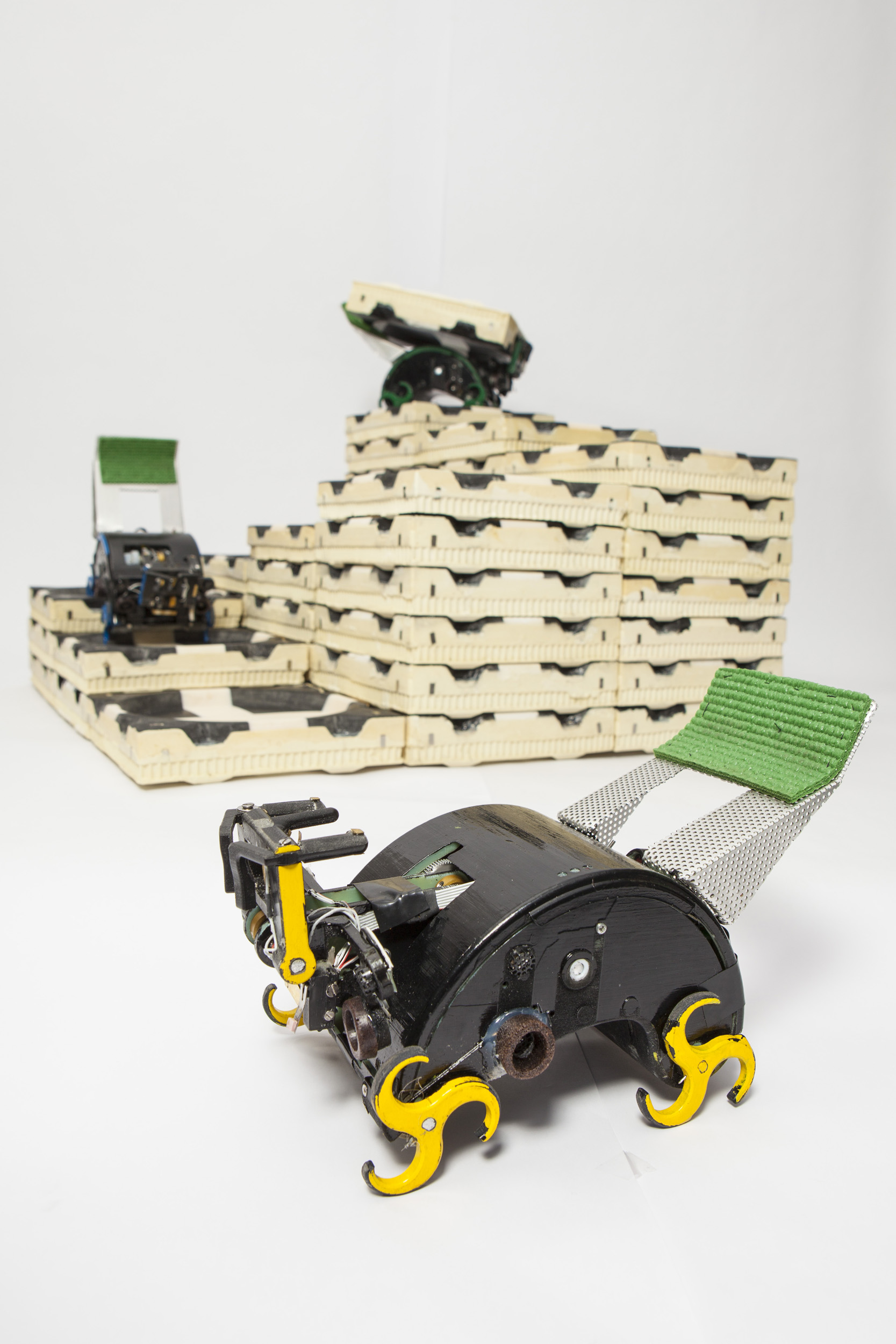
“No matter what kind of agent — ant, human being, or robot — there’s always a limit to what an individual can do. We transcend that by having groups. … Animals that have evolved to work in groups really take advantage of these things.”
Radhika Nagpal
Nagpal has found models in termites in Namibia and army ants in Panama, social insects that manage challenging tasks without central coordination.
“There are examples in nature where the coordination required is very small, so we’re using that,” Nagpal said. “That might make it possible to have many cooperating parts. The parts don’t have to be complicated, and the coordination doesn’t have to be complicated, but you can still achieve complex goals.”
Among the machines Nagpal has developed is the diminutive kilobot, programmed to behave according to simple guidelines, such as the position and behavior of neighbors. Kilobot swarms can perform complex tasks — in one demonstration they formed themselves into a starfish shape — that are not dependent on a sophisticated computer brain or a system of leaders and followers. Her group has also developed termite-inspired robots that work together on user-specified block structures.
“We can produce rules that will cause them to always build the correct structure,” Nagpal said. “And it doesn’t matter if they’re 10 or five or 50, and it doesn’t matter that they don’t know where the other ones are, and it doesn’t matter what order they’re in.”
Nagpal sees potential applications in disaster response, exploration, and with environmental sensors. Robots following simple rules could create walls of sandbags, while the inexpensive schools of robotic fish being developed in her lab could someday probe the ocean floor, supplementing or replacing the deployment of costly submersibles that can explore only one place at a time.
The development of the kilobot is an outgrowth of a rapid advancement of technology that has not only increased the sophistication of cutting-edge systems, but also dramatically lowered the price of off-the-shelf components, Nagpal noted.
“I originally thought I would never have hardware,” she said. “But the reason I thought that was a robot cost $100,000. [Today] I can build novel robots for a couple of hundred dollars. That’s a routine thing in my lab. I have a thousand robots, at $20 [each].”
Nagpal has licensed kilobot technology to K-Team, a manufacturer of small mobile robots. Today, 10 other labs around the world own kilobots, and two have 1,000-kilobot swarms.
“It’s super amazing, because all these things people are imagining doing with the kilobot system, I would never have thought of. Now it’s a vibrant research area,” Nagpal said.
The octopus has long been a source of inspiration in soft robotics because it performs feats of strength and dexterity with no internal skeleton. Powered by a chemical reaction controlled by microfluidics, the 3D-printed Octobot, from Robert Wood’s and Jennifer Lewis’ labs, has no electronics.
Photo by Lori Sanders
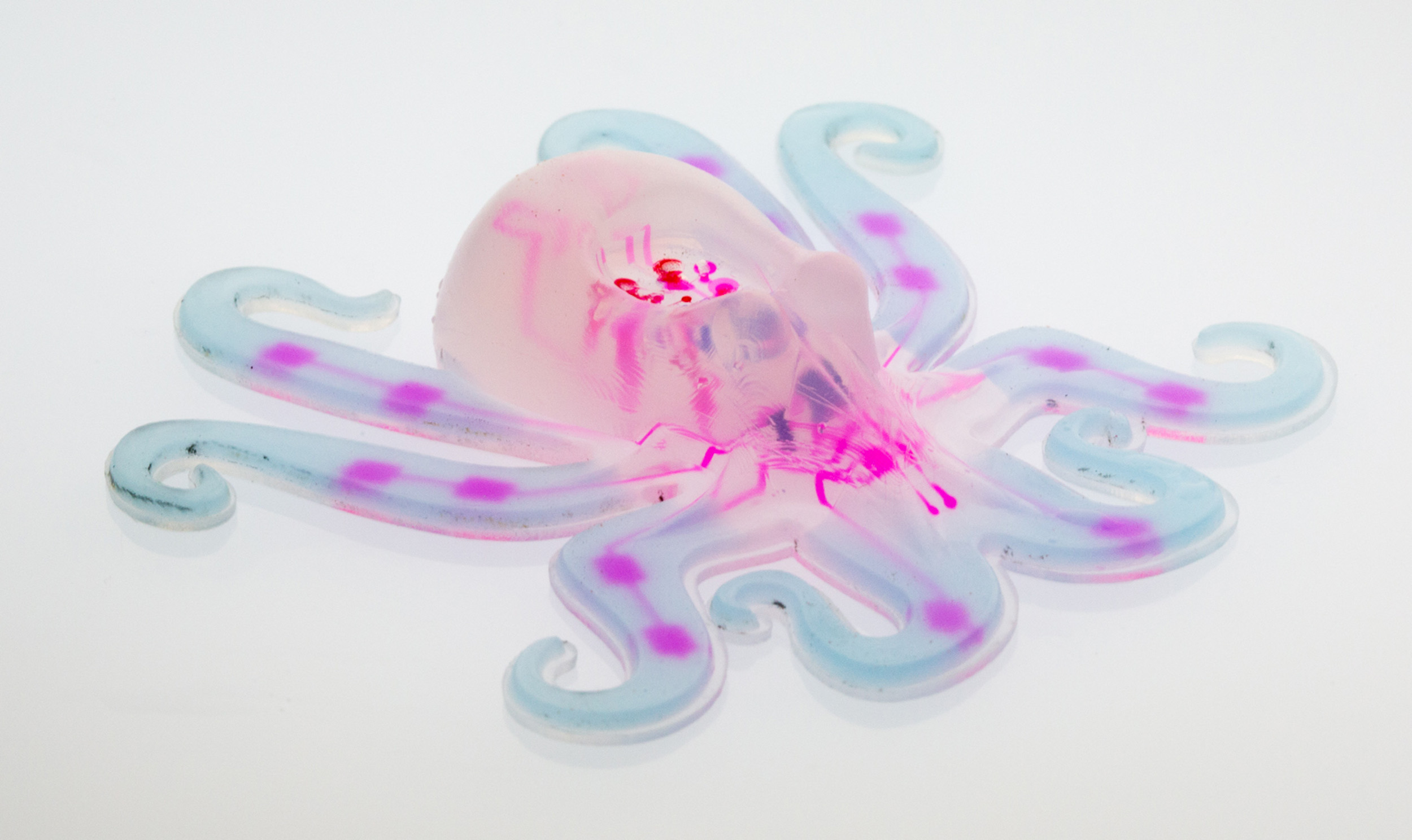
Tomorrow’s innovators
While faculty members are developing the next wave of robots, students are gaining the knowledge and experience to build the machines of the second half of the 21st century. Budding innovators learn as interns, through extracurriculars such as the Harvard Undergraduate Robotics Club, and in the classroom. A search of Harvard’s course catalog for “robot” returns options in microrobotics, artificial intelligence, control theory, and more.
“Informal Robotics: New Paradigms for Design and Construction,” taught by Chuck Hoberman, a lecturer in architecture at Harvard’s Graduate School of Design, illustrates just how far the field has come. Instead of building complex machines in a high-tech lab, students merge everyday materials with inexpensive computer parts to build robots that can sense and respond to surrounding stimuli.
“A major goal of the course is getting students to think in a different way,” Hoberman said. “You might be fooled, because these devices are paper and plastic, that there’s not a lot of engineering rigor going into it. Using rapid prototyping technologies and off-the-shelf electronics, our students can make a piece of paper walk across the room and adjust its path while sensing its surroundings. The moment of truth is when they turn their device on and it takes on animate life — it’s such a great experience for young designers.”
Students also get hands-on learning experiences outside the classroom. Members of the Harvard Undergraduate Robotics Club last year tackled a series of design challenges, including building an autonomous maze-solving robot, an unmanned aerial robot, and a wheeled robot that uses feedback controls to maintain balance.
Members say that though each individual brings particular expertise to the club — computer science, mechanical engineering, electrical engineering — robotics is such an interdisciplinary pursuit that almost everyone ventures beyond his or her expertise.
Membership in the club “had a huge impact on what I think about doing,” said Shaan Erickson ’17, who wants to marry his passions for cars and robotics in the auto industry. “It opened my eyes to an entirely different field. … I look forward to adding my own contribution to it.”
Funding for the research described in this article comes in part from the Wyss Institute for Biologically Inspired Engineering and from federal agencies such as the Department of Energy, the National Science Foundation, and the Defense Advanced Research Projects Agency.